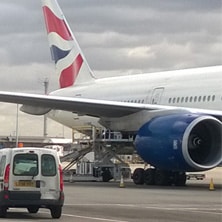
There is a significant benefit to GSE Pooling for airports, where studies suggest that planning the use of a pool of ground service equipment for use by all ground handlers, instead of the usual method of individual ownership and storage, can reduce the space used in the apron by up to 24%.
What is Ground Services Pooling?
Conventionally, Ground Services Equipment (GSE) are all owned or leased by the individual ground handlers with contracts to various airlines. This includes equipment such as baggage trains, stairs, fuel trucks, conveyors, lifters, catering lorries, cargo lorries, toilet service units and portable water – all equipment necessary to service and maintain aircraft at terminals.
Every contractor owns and stores the necessary equipment to do their job for each airline. However, due to differing peak requirements from airlines and handlers, this can lead more GSE being stored around the apron than is actually needed at any one time.
If GSE equipment were pooled, therefore owned by the airport or Airline Operating Committee (AOC) and stored centrally, then leased to each ground handler as and when they needed it, the demand for storage would be much less.
This is the major advantage of GSE Pooling. As well as space saving airside, another benefit can be cost savings. Less equipment is required, therefore less is spent on purchasing and maintaining.
What do you need to consider when implementing GSE Pooling?
As AiQ Consulting have been advising and guiding airports, airlines and the ground handlers on the initiative, we are also aware of the practicalities of implementation.
The first step is ensuring that this is the right cost and space saving step for the airport. Our experience in Apron Modeling and GSE simulations mean we can quantify the benefits of GSE Pooling to airports, AOCs and Ground Handlers, through detailed but easy to analyse models. Collecting data and running simulations of the apron, to review the results of GSE Pooling before any changes take place, allows the airport to know that GSE Pooling is the right step and how it will work within their apron.
This simulation and data collection can also feed into the tender stages, where detail specifications are needed. This can also be a benefit to bidders, allowing them to refine and/or quantify requirements for their needs.
You do have to consider the management time and cost in pooling the equipment. GSE Pooling needs to be managed efficiently to make it work. Some Ground Handlers may also require their equipment to be guaranteed, and available only to them. This obviously reduces the available stock to other handlers so can impact on the cost and efficiency savings.
Every airport has different requirements, and the contracts specifying GSE Pooling may focus on varying elements, such as cost or service. AiQ Consulting’s experience airside, as well as our bespoke simulation modeling tools, allows us to guide both the clients and suppliers through the process to the most efficient outcome.
To find out more about the benefits of GSE Pooling, and how AiQ Consulting can assist in the process, contact us today.