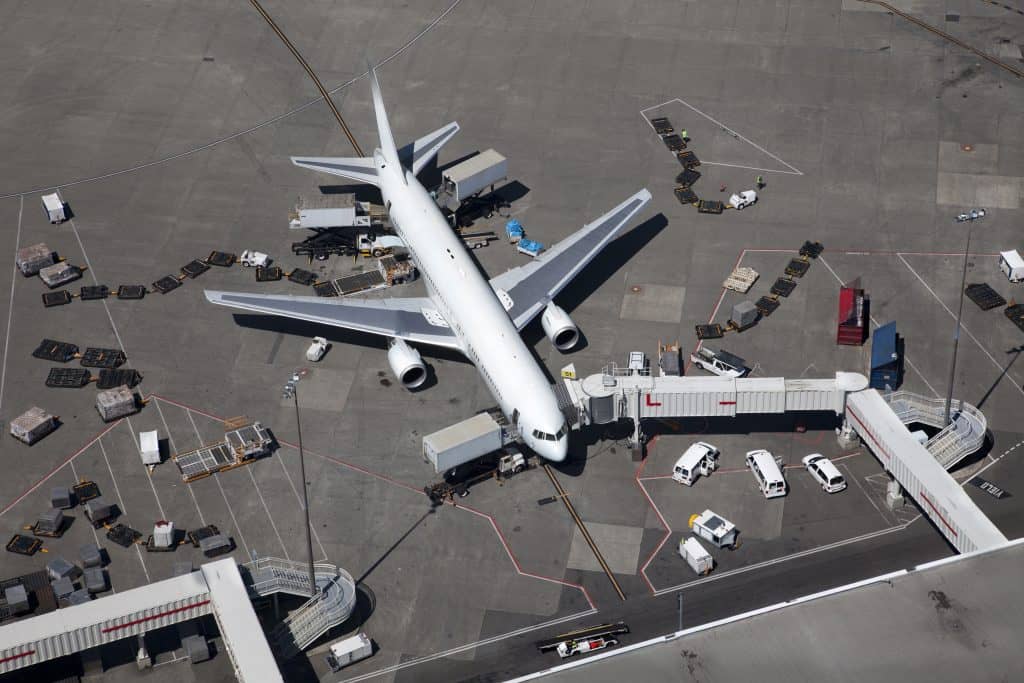
Ground Support Equipment (GSE) is a hot topic amongst airports internationally, as more and more airports and Airline Operating Committees (AOC) choose to use the initiative to save on cost and space. AiQ Consulting has been advising and guiding airports, airlines and the ground handlers themselves to find the benefits of pooling ground services equipment whilst minimising the effect felt by management of the service.
What is Ground Support Equipment?
Ground Support Equipment covers all equipment necessary to service and maintain aircraft at terminals. This can include baggage trains, stairs, fuel trucks, conveyors, lifters, catering lorries, cargo lorries, toilet service units and portable water.
Traditionally, these are all owned or leased by the individual ground handlers with contracts to various airlines. However, due to differing peak requirements from airlines and handlers, this can lead to twice as much equipment being around the apron than is actually needed. For example, if one airline peaked in the late morning, and another in the late afternoon, but they used different ground handlers for various contracts, both sets of ground handlers’ equipment must be used and stored around the terminal throughout the day.
What are the benefits of GSE Pooling?
GSE Pooling means having a central source for equipment to be used by all ground handlers regardless of contracts throughout the day. This means less equipment on the apron and less cost throughout.
The key benefits for airports or AOCs that run this system are cost and space savings. Not only is less equipment required for general day-to-day use, but there are also fewer requirements for contingency equipment. Ground handlers generally hold surplus equipment in case of unexpected peaks or problems, but holding a central stock generally reduces the need for extra.
Therefore, one of the major advantages is space airside. For example, for a 20mppa terminal, analysis shows that equipment can be reduced by up to 24%. This space-saving is also a costly one, as obviously as less equipment is required, less is spent on purchasing and maintaining.
What are the disadvantages?
The only real concern some operators have with GSE Pooling is the management time and cost of pooling the equipment. The operation needs to be managed efficiently to make it work. Some Ground Handlers may also require their equipment to be guaranteed, and available only to them. This obviously reduces the available stock to other handlers so can impact the cost and efficiency savings.
How can AiQ Consulting Help?
Through our contract as Airside Operations Planners at Heathrow, as well as our various projects in other airports internationally, AiQ have a great deal of experience in Apron Modelling and GSE simulations. We can quantify the benefits of GSE Pooling to airports, AOCs and Ground Handlers, through detailed but easy to analyse models.
We also can assist airports and AOCs in their tender documents, by providing detailed specifications, and helping bidders to refine and/or quantify requirements for their needs.
Every airport has different requirements, and the contracts specifying GSE Pooling may focus on varying elements, such as cost or service. AiQ Consulting’s experience airside, as well as our bespoke simulation modelling tools, allows us to guide both the clients and suppliers through the process to the most efficient outcome.
To find out more about the benefits of GSE Pooling, and how AiQ Consulting can assist in the process, contact us today.